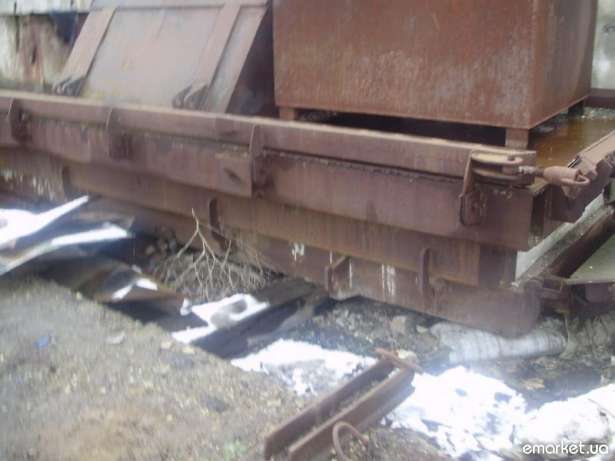
Пенобетонные блоки можно производить разными способами, но основных способов всего три. Отметим их плюсы и минусы:
1. Заливают разборные формы и пенобетон оставляют застывать на 12 часов. Затем форму разбирают, достают готовые блоки и отправляют их на просушку.
Такая технология экономически целесообразна при небольших объемах производства, до 40 куб.м. в день. Плюсы: простота производства и небольшие вложения. Минусы: привязанность к типоразмерам.
2. Заливают большие массивы в форму объемом около 3 куб м. Через 14 часов весь массив подается на автоматическую резку, где он распиливается на блоки нужного размера.
Это высокотехнологичный и производительный метод. Массив пенобетона можно разрезать на блоки любых типоразмеров. Минусы: дорогое оборудование, отходы - крошки от пиления.
3. Заливают неразборные кассетные формы и через 8 часов их подают в установку автоматической распалубки. Здесь блоки выдавливаются на поддон.
Это простой и производительный метод. Минус: установка автоматической распалубки не перенастраивается на другие типоразмеры блоков.
Итак, ясно, что при небольших объемах производства пенобетонных блоков наиболее целесообразен первый способ - заливка в разборные кассетные формы. Распространение получили три вида кассетных форм:
1. Формы фанерные
Такие формы дешевы и отличаются небольшим весом, но ни в коем случае не подходят для промышленного применения, так как размокают, легко повреждаются и служат не больше 2 месяцев. Фанерные формы можно использовать лишь при изготовлении небольшого количества блоков для себя.
2. Формы металлические без основания
Такие формы изготавливаются из металла толщиной 4 мм с помощью аппарата лазерной резки. Устанавливаются на какую-либо ровную поверхность. Для промышленного производства такие формы также не подходят из-за недостатков конструкции:
- тонкий металл гнется
- без стягивающих боковых креплений форма "гуляет"
- выгибается длинный боковой лист и блоки выходят "горбатыми"
3. Формы металлические с основанием
Только такие формы хорошо зарекомендовали себя в производстве. Они должны удовлетворять следующим условиям:
- для боковых пластин и днища используется металл 6 мм
- для петель, держащих боковины, используется металл 8 мм
- для внутренних перегородок используется металл: 4 мм для коротких и 6 мм для длинных
- основание укреплено швеллером
Такие формы долговечны и хорошо подходят для производства качественной продукции.